Injection Compression Molding

Injection compression molding ensures high-precision, stress-free, and dimensionally stable parts. VDAC offers advanced tooling, process optimization, and automation to deliver superior-quality components with enhanced durability, efficiency, and cost-effectiveness for various industries.
​
What We Offer
Application
Our expertise ensures durable, high-performance components tailored for automotive, optical, and industrial applications through advanced automation and process optimization.

The Process
Injection compression molding is an advanced manufacturing technique that combines the principles of injection molding and compression molding to produce high-precision, thin-walled, and complex plastic components. Unlike traditional injection molding, where molten plastic is injected into a fully closed mold, injection compression molding introduces the material into a partially open mold before it is compressed shut. This process allows for better material flow, reduced internal stress, and improved part consistency. By evenly distributing pressure across the molded component, this technique is ideal for applications requiring high dimensional accuracy, such as optical lenses, automotive components, and polycarbonate glazing.
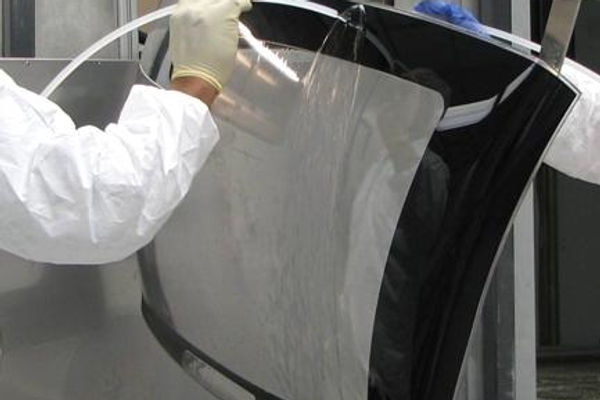
The Advantage
The benefits of injection compression molding extend beyond precision and efficiency. By applying controlled compression, this technique significantly reduces molded-in stress and enhances mechanical properties, resulting in more durable and dimensionally stable parts. Additionally, it allows for thinner wall sections without compromising strength, making it a cost-effective solution for lightweight applications. This process also improves material distribution, reducing defects such as sink marks, flow lines, or birefringence in optical applications. With VDAC’s expertise, businesses can achieve greater production efficiency, lower material waste, and enhanced product performance, making injection compression molding the ideal choice for high-quality, high-precision plastic manufacturing.
4o
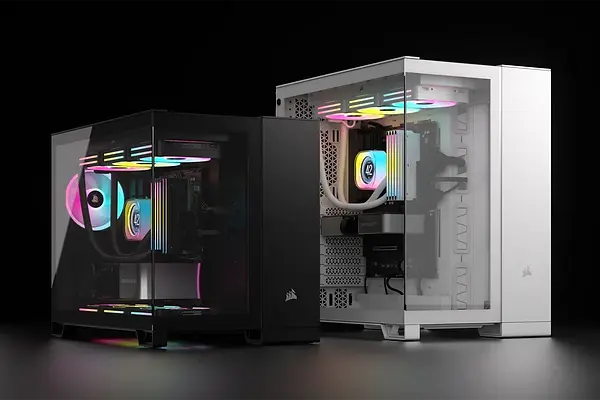
At VDAC, we leverage state-of-the-art injection compression molding technology to deliver superior quality products tailored to industry-specific requirements. Our expertise in tooling design, precision control, and process optimization ensures that each molded part meets the highest standards of accuracy and durability. We specialize in producing intricate components with reduced warpage, enhanced surface finish, and minimal residual stress. Additionally, our advanced automation systems and in-mold sensors allow us to monitor and control each stage of the molding process, ensuring consistent output and maximum production efficiency. Whether you need high-performance automotive trims, lightweight structural components, or optical-grade plastic parts, VDAC provides customized solutions to meet your exact specifications.
Project Assessment & Quotation
Production & Manufaturing
Deliver & Aftersales Service
Work With Us Now
Get started with VDAC by submitting your project details. Follow our simple process—from sharing your design to receiving a precise quotation, high-quality production, and reliable after-sales support. Upload your files and let us help bring your project to life with precision and efficiency.
Submit Your Requirement
Upload your 3D CAD file or provide technical drawings, along with details of your production requirements, including materials, quantity, and process specifications.
​
​Supported file formats:
STEP, IGES, STL, and more.
We offer design optimization recommendations to enhance manufacturability and efficiency. Detailed cost breakdown and estimated delivery timeline will also be provided.
We specialize in precision mold design and fabrication, ensuring high-accuracy development for optimal performance. Our advanced processing services include initial design, prototyping by 3D printing or CNC milling, mold production, finished parts, part assembling, and other innovative manufacturing solutions to meet diverse production need.
We ensure timely delivery through efficient production processes and professional project management to keep your projects on schedule. Our continuous support includes mold maintenance, design modifications, and repeat production services, guaranteeing long-term reliability and seamless operations.